In recent decades, rapid population growth has led to a significant increase in meat demand. To handle the high meat demand, meat supply chain management plays a key role. To be effective, a strong meat supply chain network needs to have a cost-effective design that helps make the best strategic and tactical decisions including but limited to decisions about the locations and allocation of relevant facilities in the network, as well as the optimal quantities of products that are transported in each echelon of the network. The good news is that the Decision Optimization technologies help supply chain managers of meat and poultry companies instantly make the best decisions that lead to their goals such as the maximum revenue and minimum cost. In this article, we first briefly overview the key features of meat supply chains. Then, we will introduce eight effective optimization solutions to increase their productivity and profitability.
1. Overview of Meat Supply Chains
This section introduces pig supply chains as an example of meat supply chains and talks about their features. We can apply these supply chains to other types of meat and poultry (e.g., beef, chicken, etc.) with minor modifications.
Decision-making in the pig industry has been migrating from individual farmers to pig supply chain managers. In this sense, increasing attention has been placed on the design, performance, and coordination of a set of agents operating inside a pig supply chain with a complete chain vision of pig production. The pig supply chain includes organizations in charge of procurement, production, slaughtering, processing, distribution, and marketing of pork, and its by-products to the final consumers, as shown in the following Figure.
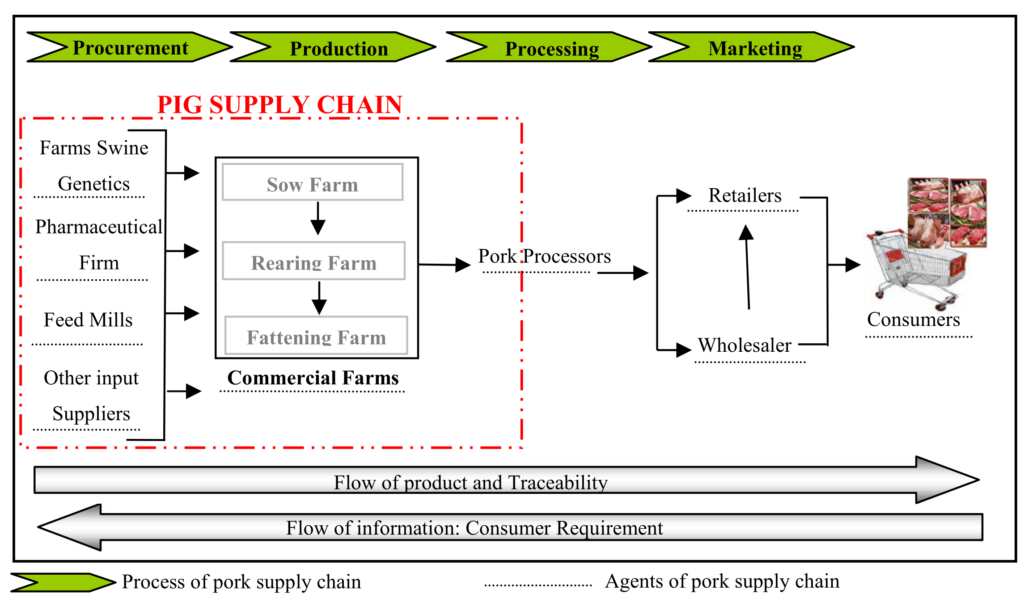
The main processes of a pig supply chain are:
- Procurement: Procurement is the process of providing raw materials for pig production such as concentrates, medicines, semen, and gilts. Feed mills, pharmaceutical firms, and selection farms are the main agents at this stage.
- Pig Production: Pig production is structured through three phases: 1) producing piglets; 2) rearing the piglets; 3) fattening the pigs and delivering them to the slaughterhouse. For each step, a set of specialized farms, including sow farms, rearing farms, and fattening farms, respectively, are involved.
- Slaughtering and Processing: The slaughtering process involves waiting before stunning, slaughtering, carcass classification, and chilling. Sometimes carcasses are marketed as a whole piece, particularly for international trading, or more frequently processed further by pork processors to get valuable cuts (e.g., ham, cutlet, and belly) and by-products.
- Marketing: Marketing deals with the sale and distribution of pork and its by-products to the final consumer. Wholesale and retail firms are part of the marketing stage. Their main functions are breaking bulk, allocating products to stores, retail packing, pricing, and displaying labels.
2. How Optimization Can Help
The planning decisions in pig supply chains are tackled at independent stages, as shown in the following Figure:
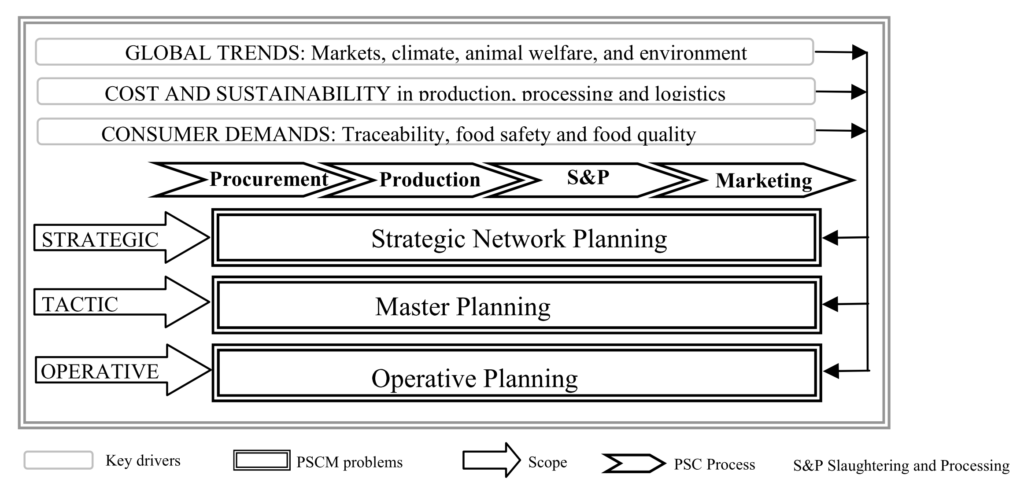
With this background, here are some examples of how optimization can help pork processor companies:
- Optimal Planning of Pig Transfers Along a Pig Supply Chain: The pork supply chain management involves coordinating sets of farm units at different phases, which is a complicated task. We can develop optimization models that maximize the total revenue of the pig supply chain concerning the costs of animal feeding, doses of insemination, labor, transportation, veterinary expenses, etc., over a multi-year planning horizon on a weekly basis. These optimization models can provide the best solution for production planning, that is, for example, the flow of animals among farms and towards slaughterhouses, the number of animals to be produced and transferred at each phase and stage, the number of trucks, and optimal replacement policy for each sow farm, as well as the optimal delivery of fattened pigs to slaughterhouses.
2) Optimal Planning of Sow Replacement: Livestock systems have a cyclic nature. In most cases, an animal is inserted into the herd and, after some cyclic periods (lactations, parity, feeding cycle), replaced with a new animal. Decisions regarding which cycle and when to replace the animal within the cycle have to be made. The sow replacement problem is one of the most complex decisions in pig production. The optimal replacement policy refers to when the sow production declines and should be replaced by a young sow with a higher revenue expectation. Besides the optimal replacement policy, the sow replacement problem determines herd structure, the life expectancy of sows, annual replacement rate, piglet production capacity, and other important key factors in herd management. Furthermore, the replacement has not only impacts on sow farm performance but also the performance downstream in the pig supply chain. We can develop Markov Decision Processes optimization models to model livestock decision problems such as the sow replacement problem.
3) Optimal Facility Location Plans: The location of processing facilities is affected by the closeness of consumption and distribution centers. For this reason, studies of cattle and livestock logistics also have focused on infrastructure and investment decisions, often taking the form of facility location and transshipment problems. A common problem in pork/beef logistics is determining the optimal size and location of slaughterhouses. We can develop facility location optimization models to determine the optimal locations of the slaughterhouse (or farms) and their optimal processing capacities. For instance, the location of a slaughterhouse when several pig farms are already operating is an optimization problem. In general, the location problem in the pork supply chain involves a trade-off between the number of facilities and associated transportation costs.
4) Optimal Meat and Livestock Transportation Plans: Transportation optimization has been a concern of beef/pork producers in the past years. We can develop network optimization models to determine the optimal geographic flows of livestock and meat for interregional transportation of meat and livestock in the United States.
5) Optimal Pig Supply Chain Network Design: Strategic or long-term planning decisions aim to identify the optimal strategic network of the supply chain. Within the pork context, these problems emerged to determine the number, location, allocation, capacity, and type of pig farms and slaughterhouses to be integrated, the set of suppliers to be selected, and the transportation channels to be used. We can address all of these problems by developing network optimization models.
6) Optimal Delivery to Slaughterhouses of Fattened Pigs: Fattening farms host the last stage of pig production. Pigs arrive from rearing farms and are grouped and managed in batches. Pigs are fed until they reach a specific marketing weight. The usual planning problem is related to the optimal delivery to the slaughterhouse of fattened pigs that maximizes the farm’s profit. The value of fattened pigs depends on carcass weight and meat quality measured in terms of lean and fat percentage. We can define this problem as an optimization model and solve the model to obtain optimal plans.
7) Optimal Production Planning: Tactical or middle-term planning decisions aim to optimally coordinate, integrate and synchronize the flow of information and marketable product along the supply chain. Thus, the chain manager coordinates the flow of replenishment gilts, insemination doses, piglets, and fattened pigs, looking for the most efficient way to satisfy the demand forecast over a medium-term planning interval. The master planning supports contract agreements, specifying operations guidelines for the chain agents such as production goals and targets and supply quotas. Supply and demand must be matched to generate the highest profit. Some of these aspects representing the integration and coordination between chain agents can be included in some optimization and predictive models.
8) Optimal Operational Decisions: Operational or short-term planning decisions in a pig supply chain aim to handle incoming customer orders in the best possible manner. Decisions at the operational level enclose scheduling problems related to the flow of product or information through the chain following the guidelines of the master plan. Hence, decisions at the operational level in the pig supply chain involve tasks performed every day, such as determining the sows to be inseminated, culling of sows, weaning piglets, and selection of pigs to send to slaughtering, and their transportation. Vehicle routing problems, distribution, and transportation problems are usually set at this level. The nature of these problems involves a model design with a mixture of scheduling (e.g., farms to visit first for the collection of animals) and routing (e.g., trucks leaving the slaughterhouse to collect and transport animals back). The decision-making must consider the slaughter production plan and the lairage capacity as well as the animal welfare restrictions. Thereby, these problems can be formulated as a combination of vehicle routing and scheduling optimization problems extended with constraints regarding production and inventory as well as animal welfare dispositions.