Dairy product consumption is rising globally. Milk is still the highest consumed dairy product in the world, followed by butter and cheese. The growing consumption brings pressure to the dairy product industry for more enhanced processes. On the other hand, dairy product companies should focus on quality, compliance with product safety regulations, and hygiene in the process. Therefore, efficient production planning and scheduling for leveling the pace, eliminating bottlenecks, and organizing resources in the best possible way are very important. Moreover, supply chain variability, i.e, the variability of the final product quality, with difficulties to predict product quality and shelf life has a negative impact on dairy effectiveness, competitiveness, and sustainability of the system and contributes to increased insecurity in dairy supply.
To overcome these limitations, managers need state-of-the-art planning and decision-making tools that can instantly provide the best plans and decisions. This article briefly goes over the main characteristics of dairy supply chains, elaborating on their most important challenges. Then, it introduces the most efficient optimization solutions that help managers and decision-makers tackle these challenges as much as possible.Â
1. Overview of Dairy Supply Chains
Dairy supply chains have the following unique features that distinguish them from other supply chains:
- Dairy supply chains have four main elements: raw milk suppliers/farmers, milk processing plants, retailers, and end consumers.
- They include three main actors with different goals: 1) milk collection centers that aim to sell most of the collected milk; 2) dairy processors who look for maximum profit, and 3) markets that pursue customers’ demand satisfaction.
- The main difference between the dairy supply chain with other supply chains is its perishable products, which influence the whole supply chain, from getting milk at dairy plants to delivering end dairy products to consumers.
- In a dairy supply chain, the primary incoming raw material is raw milk, which is used to produce all dairy products. The amount and type of end products depend on the nutrients in raw milk. Since the nutrient content of raw milk changes during the year, the volume and type of end products also change.
- During end-product production, some other nutrients produce in an unplanned way. This nutrient is called byproducts which can be used in another part of the process. Therefore, dairy production processes are undependable, i.e., byproducts produced in one section can be used in another section of processing.
- A production site can conceptually be divided into five operational stages that all products have to pass in chronological order, as illustrated in the following Figure. The first stage receives the milk by trucks delivered from the farmers. The second stage processes the milk into dairy products and store them in large silos. In the third stage, the dairy products are packaged. In the fourth stage, all products are stored until delivery from the loading bay, which is the fifth stage.
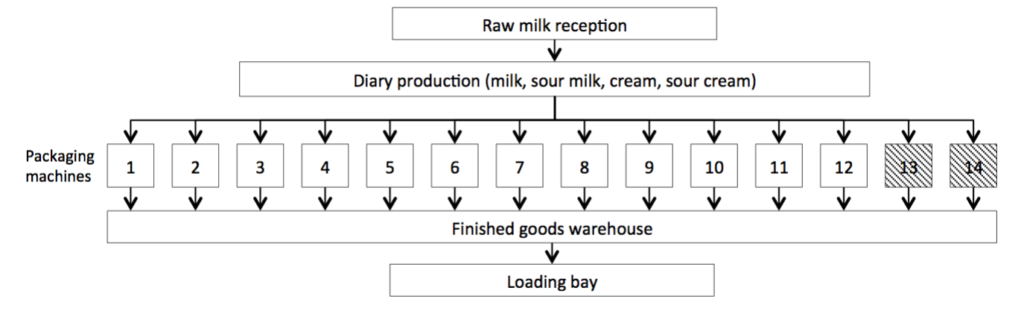
- We can consider yogurt production, which is comparable to other dairy production processes (e.g., cheese, butter and ice cream), as a production and distribution problem, as illustrated in the following Figure. The production side fundamentally corresponds to packaging and fermentation/incubation operations. The distribution side considers the storage of products and the delivery to distribution centers.

2. Challenges
The dairy product companies usually face the following challenges:
- Due to the perishable nature of dairy products, it is a challenge to manage the dairy supply chain effectively. Due to high perishability, food waste rises. Further, these products need a quick responding supply chain supported by effective coordination throughout the supply chain network. Thus, the industry’s shop-floor executives and top management need to manage their supply chain activities effectively.
- No matter how strong is the supply chain, risk and uncertainty come into the picture by disrupting the operational flow. The situation further gets complicated if the nature of the material the supply chain deals with is perishable. This is because, in this case, the material requires conditioned transportation and storage.
- Many dairy product companies are experiencing increasing transportation costs. Therefore, they seek to reduce their transportation costs while adding value to the raw milk that would be sold separately in different markets.
- Fluctuations in demand and prices of dairy products, intense competition, increased access to foreign markets, and the rules that significantly restrict performance affect dairy processes. Due to the complexity of the dairy supply chain that results from its unique features, dairy product companies need advanced methods for the efficient dairy supply chain management.
- The narrow delivery time concerning the production period often forces dairy companies to produce to stock, and large volumes must be stored before they can be delivered. Consequently, the storage occasionally gets full, resulting in production stops until some finished goods have been delivered. This problem implies rescheduling issues causing the disturbance in the production unit and, more importantly, causes delays that result in failing to deliver on time. Overall, these issues increase costs and waste and threaten dairy company’s customer relationships.
- Yogurt is a notably perishable product within the category of the dairy industry. It has a wide variety of retail cup sizes or labels, contents and special ingredients with numerous flavored and colored types. The perishability highly restricts its storage duration and delivery conditions. When it comes to producing large numbers of products from a few initial product recipes, product-dependent cleaning, sterilizing, re-tuning issues of pipes and mixing units arise to avoid contamination. Especially, long sequence-dependent setup times and high costs are considerable at yogurt production’s filling and packaging stages. They cause a noticeable reduction of available production times and increase the costs. Hence, planning and scheduling of yogurt production require specific models to support decision-making.
- A wide range of dairy products corresponds to the large diversity of consumer tastes and consumption trends. Due to factors such as high variability of raw materials, intermediate and final products, fluctuating prices, or varying processing times, production planning in the dairy industry is generally challenging. Optimizing resources and processes is the key to turning these challenges into a competitive advantage.
- Dairy product companies face uncertain milk production in planning due to several factors. Such uncertainty can lead to significant losses unless some account is taken of this in production planning. The effects of uncertainty in milk supply are important because dairy product companies sell most of their milk products through contracts arranged several months in advance of production. After the contracts have been made, the milk production in the months before they are produced and delivered may be lower than what has been forecast. If such a scenario is not considered when the contracts are made, then dairy product companies may face inadequate inventory to deliver the contracts, which incurs a high cost because it then must either breach the contract or acquire the products from a third party at considerable expense. Therefore, dairy product companies should seek tools to mitigate the effect of this uncertainty in planning.
3. How Optimization Can Help
Here are some examples of how optimization can help dairy product companies to handle their challenges:
- We can apply optimization techniques to each of the five stages mentioned in part 6 of Section 1. More specifically, the following Figure shows the main issues in dairy supply chains that can be addressed by Optimization and data analytics.
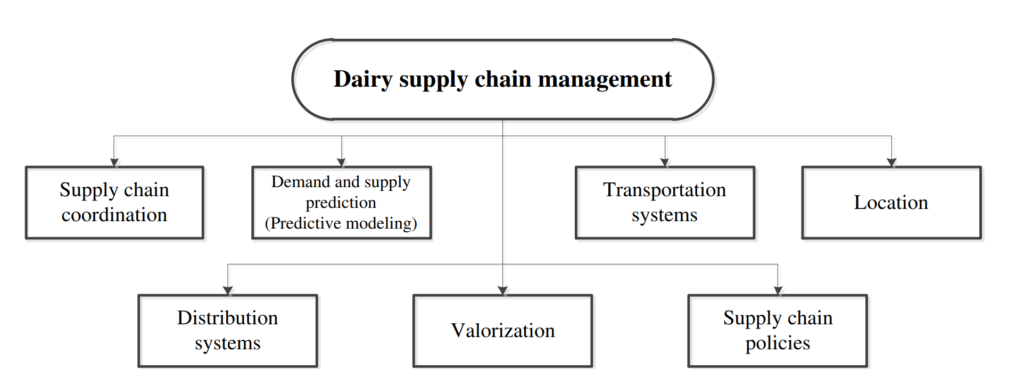
- We can develop various optimization models for uncertain milk supply, enabling dairy product companies to make better decisions in the face of uncertainty. We can first derive the forecast milk supply using predictive models or statistical forecasting models for a planning horizon. Then from this, we can derive optimization models for uncertain milk supply.
- We can develop production scheduling and distribution planning optimization models for
yogurt, cheese, butter, and ice cream production lines of the multi-product dairy plants. Production scheduling is also interrelated with a part of the transportation problem. The delivery could further compound the complexity of optimization models. For example, the objective function of a model can be the maximization of the benefit by considering the shelf-life-dependent pricing component and costs such as processing, setup, storage, overtime, backlogging, and transportation costs. The model’s key features may include sequence-dependent setup times, minimum and maximum lot sizes, overtime, shelf-life requirements, machine speeds, and dedicated production lines, typically arising in the dairy industry. The optimization models can obtain the optimal production plan for each product type, on each production line, in each period, together with the delivery plan. - We can develop network optimization models as a vehicle routing problem to find the optimal number of trucks and their optimal delivery routes to minimize the delivery time or delivery cost (i.e., development of optimal routing plans for a designated fleet of trucks).
- One of the tools used in the dairy frameworks is the dairy valorization model. To reduce food waste, there are some solutions like valorization. By valorization and recycle byproducts, it can be prevented from uncontrolled and indiscriminate dairy food waste. The valorization model is used to enhance or try to enhance the price, value, or status. The dairy valorization models can identify the best and the most economical composition of dairy products. Valorization tools are used in various fields of food supply chains such as energy, main products, byproducts, and other vital sectors of this kind of supply chain. One of the most important applications of dairy valorization models is the valorization of raw milk, which is affected by many restrictions. Some of these restrictions can be pointed to the seasonality of milk composition, the milk collected, the interdependence of the production process, the amount and type of demand and supply, current capacities, and transport streams. The contrast between the restrictions and understanding of the production process can make valorization models more comprehensive and highly functional.